Hydroforming
Is a highly versatile and special technique for machining complex components using high-precision pressure technology.
Hydroforming is a metal forming process in which a high-pressure fluid is used to form a metal blank into the shape of a tool. This process is widely used in various industries as it enables the production of complex shapes.
Automotive
This technique makes an important contribution to the production of components such as exhaust systems and structural parts. The process enables the production of intricate shapes and designs that improve vehicle performance and fuel efficiency.
For example, hydroformed exhaust systems can be designed to optimize airflow, reduce back pressure and improve engine efficiency. Similarly, hydroformed structural parts can provide greater strength and rigidity while reducing weight, which contributes to better handling and lower fuel consumption.
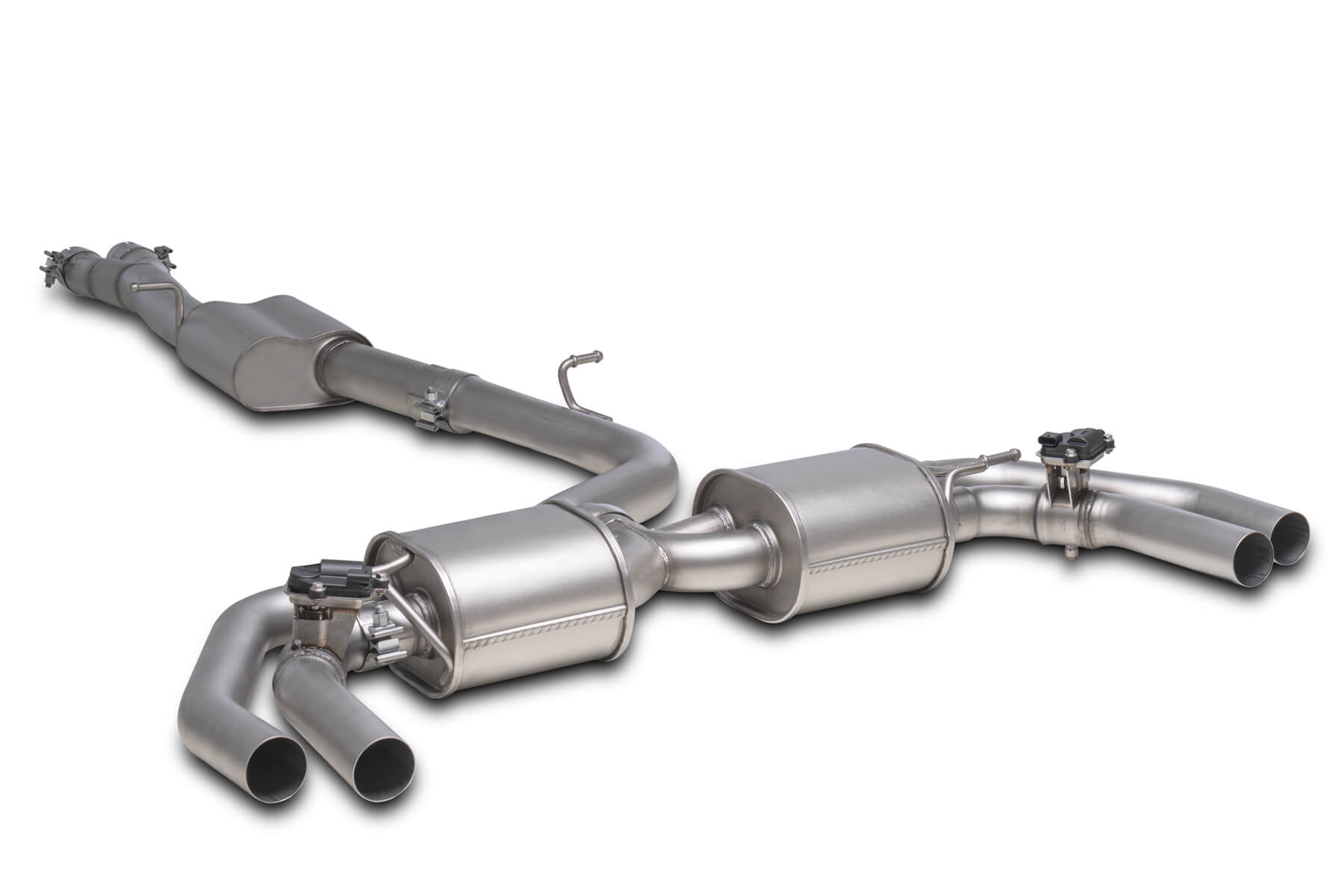
Aviation & Aerospace Industry
Hydroforming is the preferred method for manufacturing lightweight and robust parts, which are essential for aircraft and spacecraft. The process enables the production of complex, three-dimensional components with high precision and consistency.
This is particularly important in the aerospace industry, where the weight and strength of components can have a significant impact on performance and safety.
Bicycle industry
We use hydroforming to produce durable and intricately designed frames. Hydroformed bicycle frames offer greater strength and rigidity compared to conventional frames, while allowing for more creative and aerodynamic designs.
Bringing many advantages for modern frames, this results in bicycles that are both more efficient and aesthetically pleasing. Especially e-Bike manufacturers can profit of this sophicticated production process.
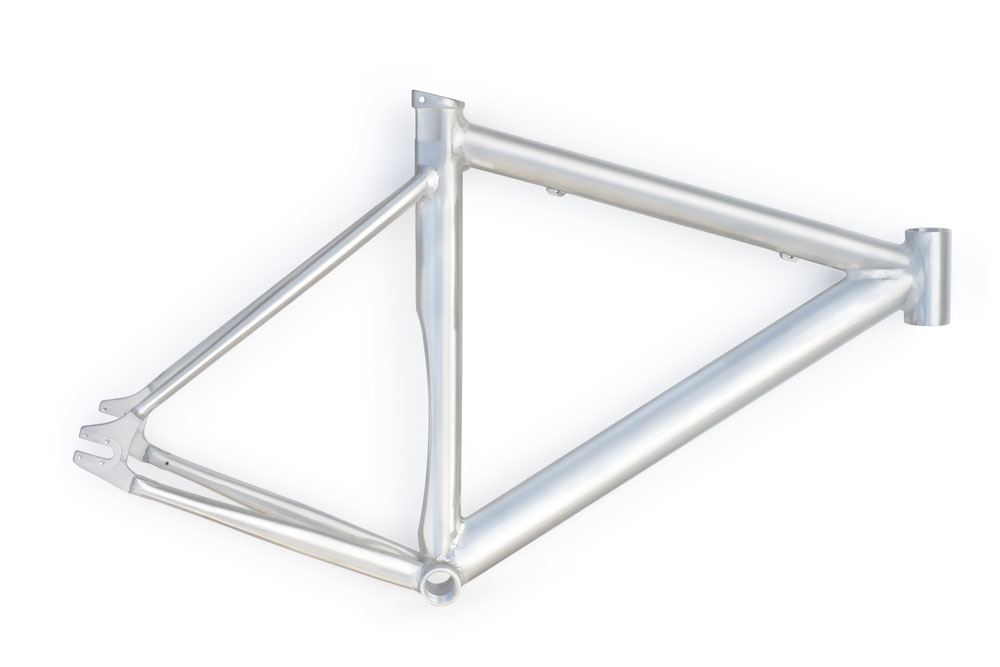
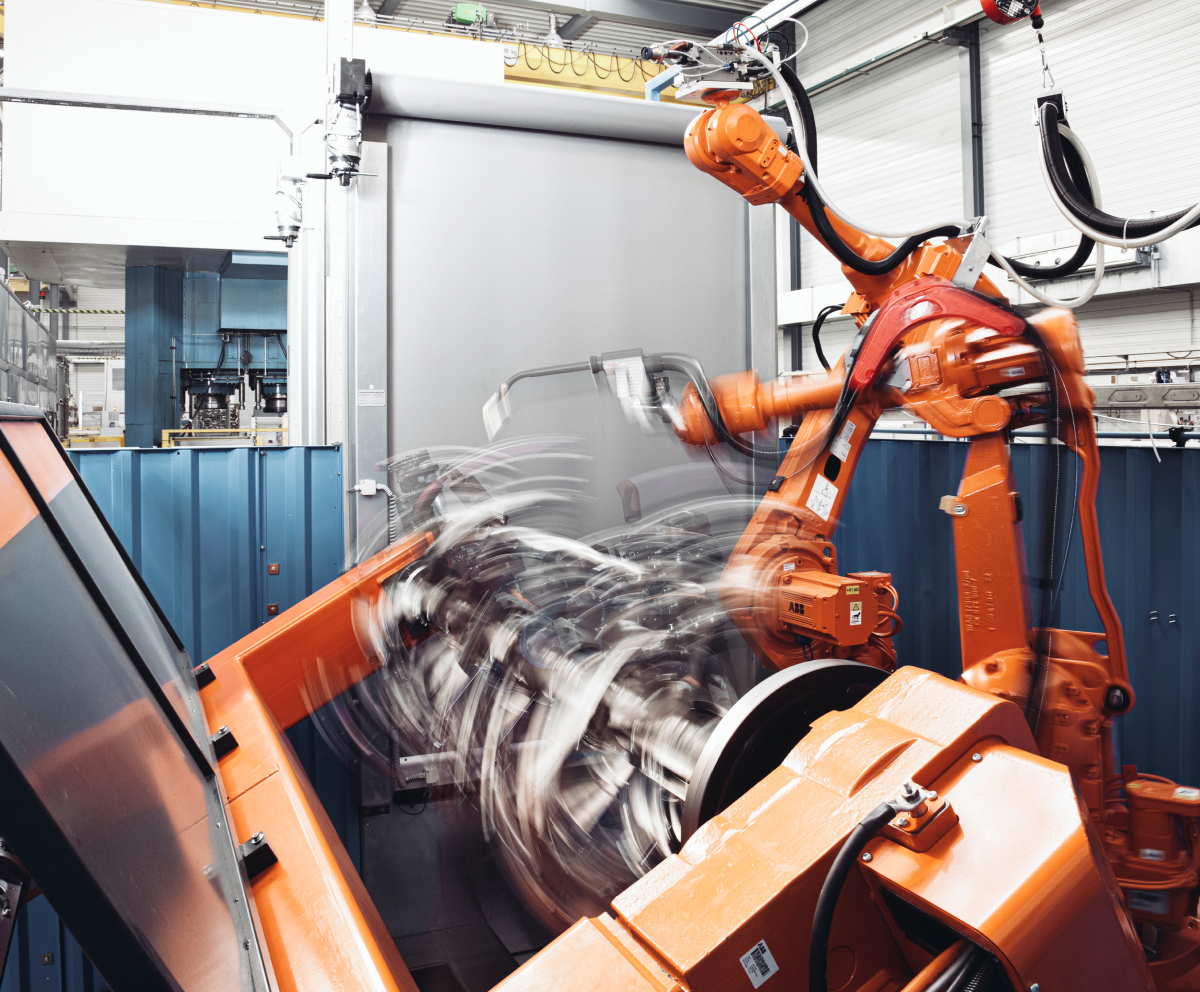
Household appliances
In the manufacturing of household appliances, hydroforming offers advantages in the production of seamless components such as washing machine drums.
The ability to form complex shapes without seams or welds can improve the durability and performance of these components. For example, a seamless washing machine drum can reduce wear and tear on clothes, improving the performance and lifespan of the appliance.
Medical sector
It is also used in the manufacturing of certain medical devices where precision and strength are of paramount importance. The process can be used to manufacture intricate components for medical devices, such as surgical instruments or implantable parts.
The high precision and durability of the hydroforming process can ensure that these components meet the stringent quality and performance standards required for medical applications.
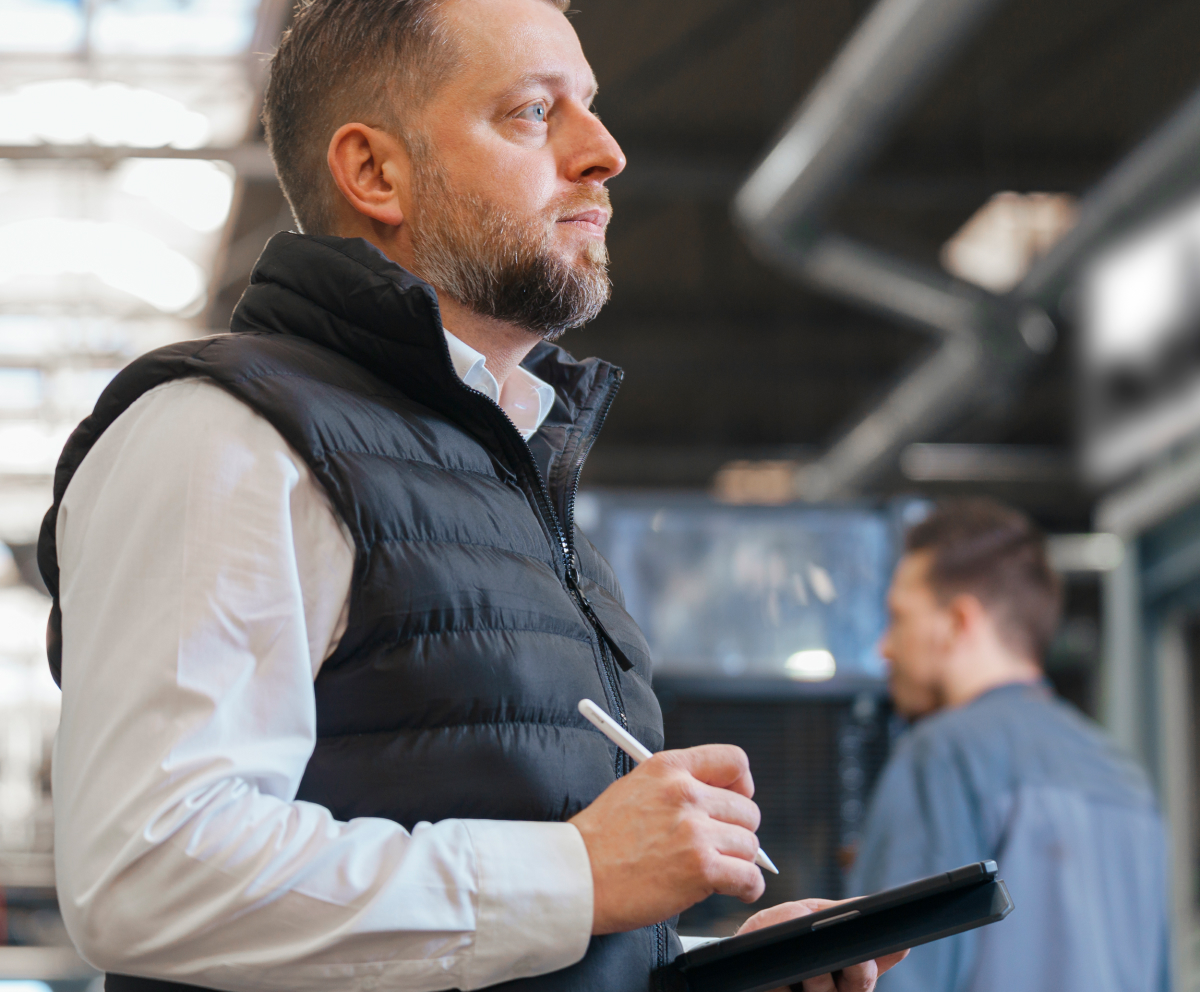
As your innovation partner for complex solutions, Metal Competencies uses hydroforming to produce high-quality, precision-manufactured components for you.
Our mission:
Optimizing your production
We optimize your processes. Costs are reduced. We are driven by quality and individuality.
Adding value
Creating complex solutions for our customers is the most important thing for us – simply our core competence.
Hydroforming FAQs
Is your part complex and made of ductile metal? Hydroforming might be ideal. For large volumes, consider stamping. Hydroforming suits smaller batches of complex parts.
Stamping wins for large volumes due to lower cost per part. Hydroforming shines for complex parts in smaller batches. Welding is generally more expensive for both but offers more flexibility in material choice.
Hydroforming is generally considered more eco-friendly. It often uses less material and energy compared to welding. However, stamping might be even better for large productions due to its high efficiency.