Brazing and Soldering
Induction Brazing is a process that uses electromagnetic fields to provide a controlled heat source for the joining of metals. This technique is particularly beneficial in the automotive industry due to its precision and efficiency.
Unleash the versatility of brazing with us. Explore high-strength bonds, perfect for dissimilar metals, intricate repairs, and beautiful finishes.
Induction Brazing
Where brazing shines: In the assembly of transmission components such as torque converters and planetary gears, induction brazing is commonly employed. The localized heating ensures that only specific areas of the assembly reach the required temperature, thereby minimizing thermal impact on surrounding materials. This contributes to the production of durable and high-performance automotive components, enhancing the overall efficiency and reliability of the vehicle.
Moreover, induction brazing offers several advantages over traditional brazing methods. It provides rapid, consistent heating, which can lead to improved production rates and lower energy consumption. The process also allows for better control over the heat source, reducing the risk of overheating and damage to the components.
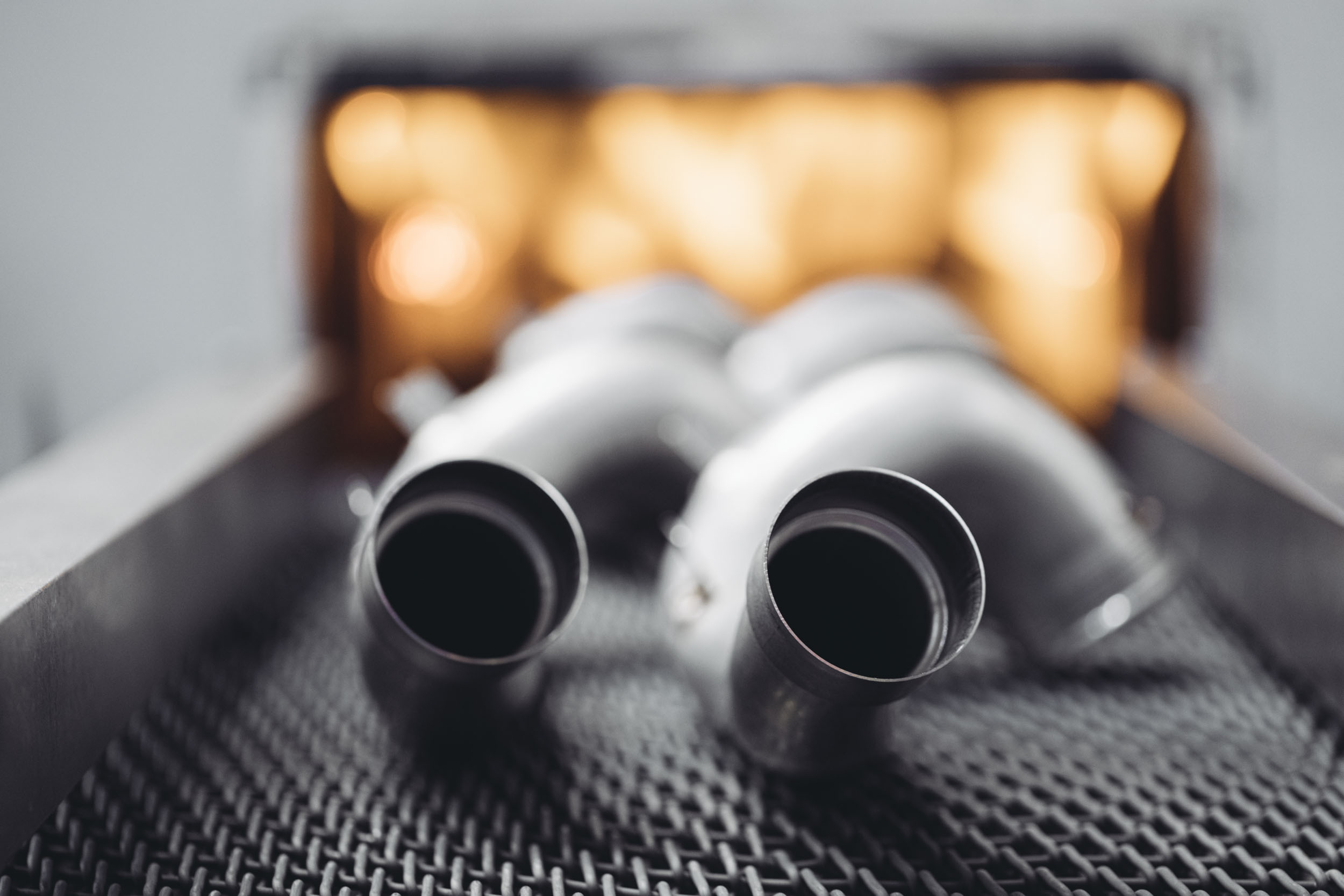
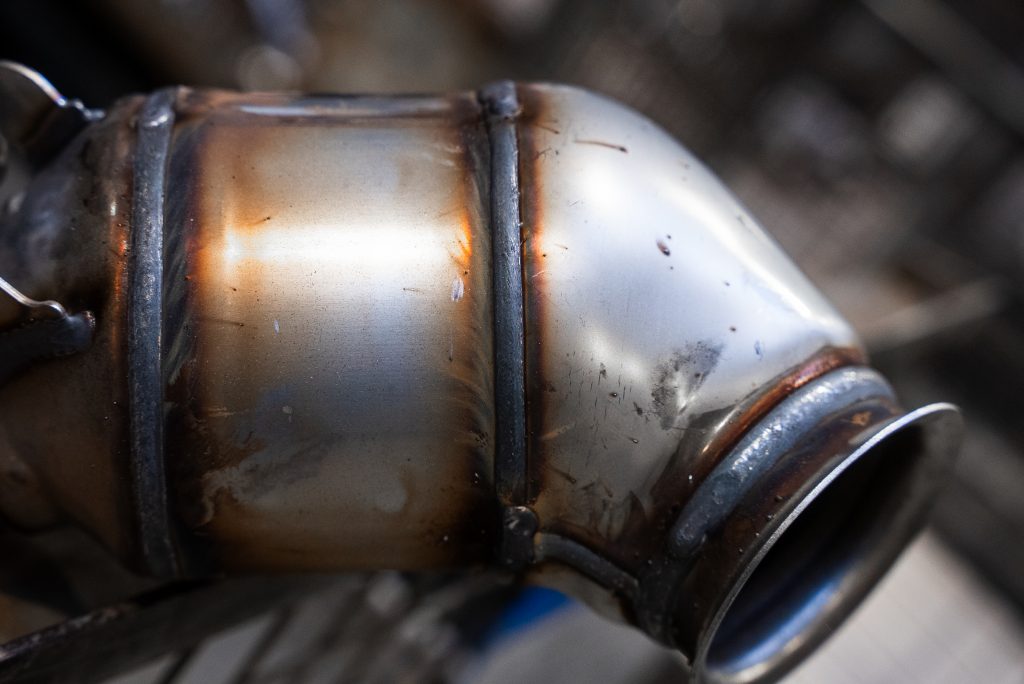
Hard Soldering
Hard Soldering, on the other hand, is a process that involves the use of a filler metal (or solder) to join pieces of metal together. In the automotive industry, hard soldering is often used to create robust joints in critical components. A example of this is the assembly of heat exchangers, where the use of silver-based solder alloys ensures a strong and reliable bond. Automotive heat exchangers, such as those in radiators and air conditioning systems, demand joints that can withstand varying temperatures and mechanical stresses. Hard soldering meets these requirements, providing durability and longevity to the soldered joints in such heat exchange components.
The process of hard soldering offers several benefits. It creates a strong bond that can withstand high temperatures and pressures, making it ideal for applications in harsh environments. Additionally, hard soldering does not require the high temperatures of welding, reducing the risk of thermal distortion and damage to the components.
In conclusion, both induction brazing and hard soldering are indispensable techniques in the automotive industry. They contribute significantly to the assembly of components that require strong, precise, and reliable joints. Whether it’s enhancing the performance of transmission systems through induction brazing or ensuring the longevity of heat exchangers with hard soldering, these joining processes play a pivotal role in manufacturing high-quality parts. As a partner for both these processes, Metal Competencies is committed to delivering the best solutions to meet the evolving needs of the automotive industry.
From industrial applications to intricate artwork, the possibilities with brazing and hard soldering are endless. Discover the perfect technique for your next project and discover our capabilities.
Our mission:
Optimizing your production
We optimize your processes. Costs are reduced. We are driven by quality and individuality.
Adding value
Creating complex solutions for our customers is the most important thing for us – simply our core competence.
Solder FAQs
Induction brazing offers more precision, efficiency and cleanliness, while soldering can be suitable for rougher work and applications with open flames.
Precise and even heat supply: Enables precise heating, minimises deformation and ensures high-quality soldered joints.
Fast process and high energy efficiency: Short soldering times, low energy consumption and reduced operating costs.
Clean and safe working environment: No open flames, smoke or soot formation, improved working conditions and an environmentally friendly process.
Reproducible results and high quality: Precise control, high reliability and suitability for complex geometries.
Versatile application possibilities: Wide range of materials, miniaturisation possible and established in various industries.
Firm connections: Ideal for high mechanical loads.
Versatile: Joins various metals and alloys.
High thermal conductivity: Predestined for thermal engineering and electronics.
Good electrical conductivity: Enables reliable current transmission.
Easy to repair: Simple disassembly and reassembly possible.
Cost-efficient: Especially for small components and limited space.
When soldering, especially in industry, various environmental standards must be adhered to in order to protect human health and the environment. These include hazardous substance regulations such as REACH and RoHS, emission regulations for air pollutants and waste water, occupational health and safety regulations and sustainability standards such as ISO 14001.
Soldering can reduce production costs in many ways. Costs can be minimised through material savings, simplified production, reduced reject rates, higher production speeds, lower maintenance costs and energy savings.