Deep Drawing
Metal deep drawing is a manufacturing process in which a sheet of metal is drawn through a punch into a die, creating a three-dimensional shape. Successful deep drawing requires careful coordination of all process parameters and precise knowledge of the material properties.
Deep drawing is frequently used in the industry as it can be used to produce parts such as body panels, fuel tanks and exhaust system components with complex and precise shapes.
Automotive
Body parts such as doors, fenders and hoods are often deep-drawn to achieve the desired contours and structural integrity. The process enables the production of complex shapes with high precision and meets the demanding standards of the industry in terms of both aesthetics and functionality. The result is components that not only fit perfectly, but also contribute to the overall aesthetic impression of the vehicle.
Fuel tanks are usually manufactured by deep drawing, which ensures a seamless and leak-proof container. The process allows for the production of a one-piece component, eliminating the need for seams or joints that could potentially leak. The result is safer and more reliable fuel storage solutions.
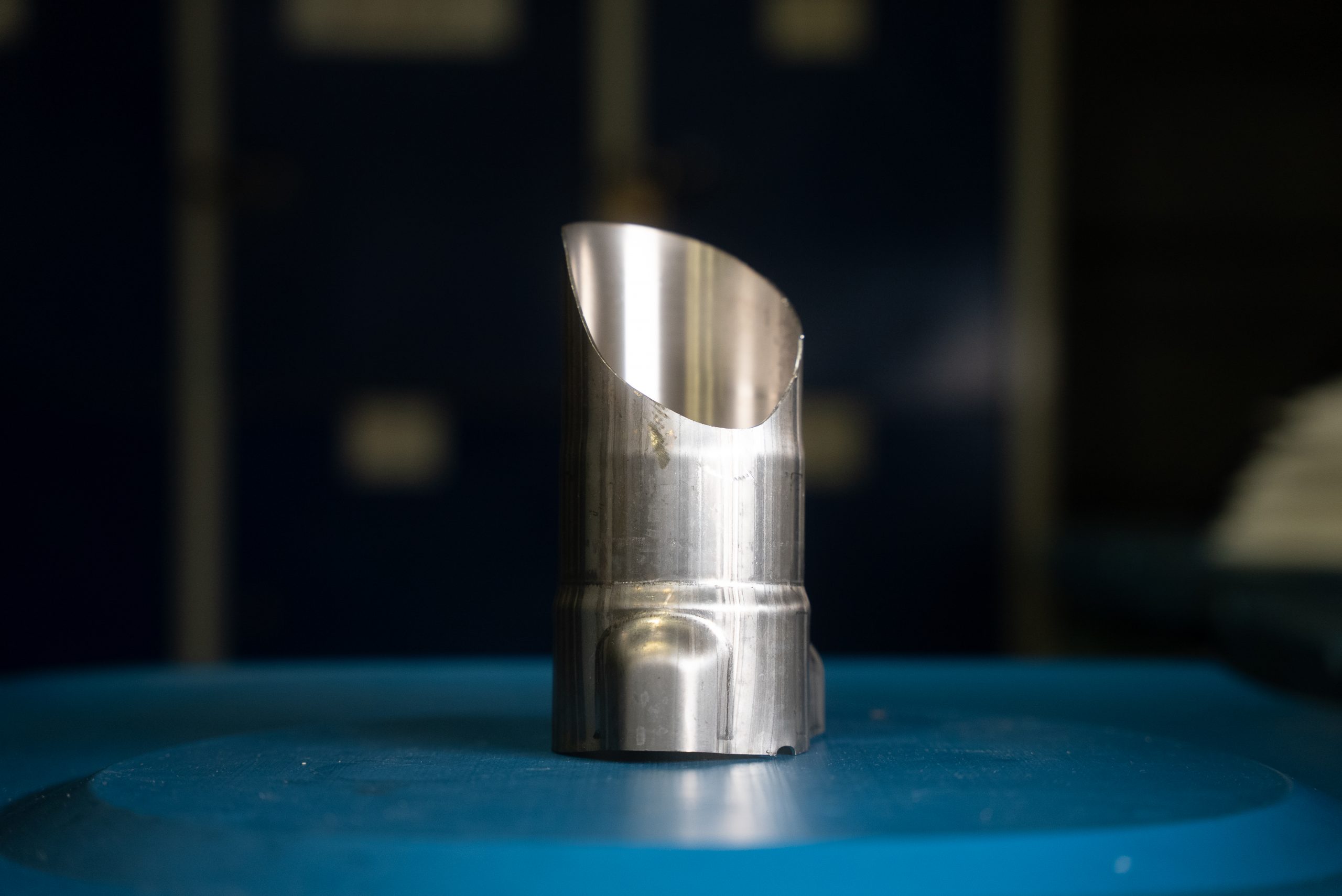
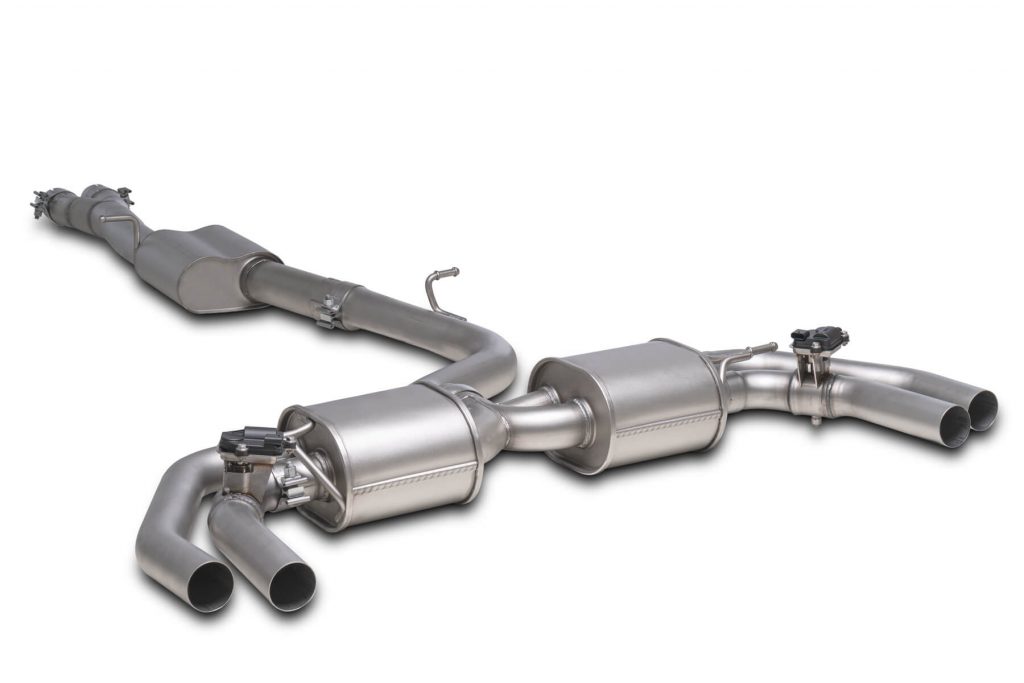
Exhaust Systems
Exhaust components, such as silencers and catalytic converters, also benefit from this process. Deep drawing enables the production of specific shapes and dimensions that are crucial for efficient performance. The process ensures that these components fit perfectly into the vehicle’s exhaust system, contributing to optimal vehicle performance and lower emissions.
Importantly it contributes to lightweighting efforts, improving the vehicle’s fuel efficiency and power-to-weight ratio. The ability to form complex shapes with high dimensional accuracy makes it an essential technique in the production of various automotive parts. The result is vehicles that are not only lighter, but also more fuel efficient and environmentally friendly.
Metal forming vs. die-cast
CO2 savings and the CO2 footprint of a product have a major influence on our parts life cycle. In order to reduce the CO2 footprint of die-cast parts and at the same time achieve cost savings, we rely on single or multi-layer forming.
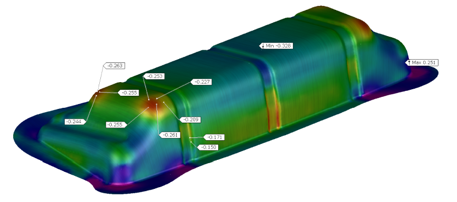
Deep drawing plays a central role in the automotive industry and Metal Competencies, with its expertise and wide range of products, is your reliable partner in this field.
Our mission:
Optimized production
We optimize your processes. Costs are reduced. We are driven by quality and individuality.
Create value
Creating complex solutions for our customers is the most important thing for us – simply our core competence.
Deep drawing FAQs
Deep drawing shapes everything from car hoods to beverage cans. It excels at complex shapes, but there’s a limit. Deep drawn parts typically have rounded bottoms and can’t have sharp corners or deep undercuts.
Deep drawing is generally cheaper for complex, high-volume parts. Stamping is best for simple, high-volume parts. Welding offers more flexibility in materials but can be expensive for complex shapes, especially for large quantities.
Deep drawing typically works best with thin to medium-thickness sheet metal. There’s a separate process called tube drawing for tubes. Material-wise, it works well with ductile metals like aluminum or copper, but may not be suitable for very hard or brittle ones.