Tube bending
Metal tube bending is a precision manufacturing process that involves manipulating cylindrical metal tubes into desired shapes without compromising their structural integrity.
This technique is commonly employed in industries such as automotive, aerospace, and construction to create components with specific curves, angles, or configurations.
Industrial use
Using specialized machinery, the metal tube is carefully bent to meet precise specifications, ensuring optimal functionality and fit within a larger assembly.
The process requires expertise to account for factors like material characteristic, bend radius, and wall thickness, resulting in versatile components used in various applications.
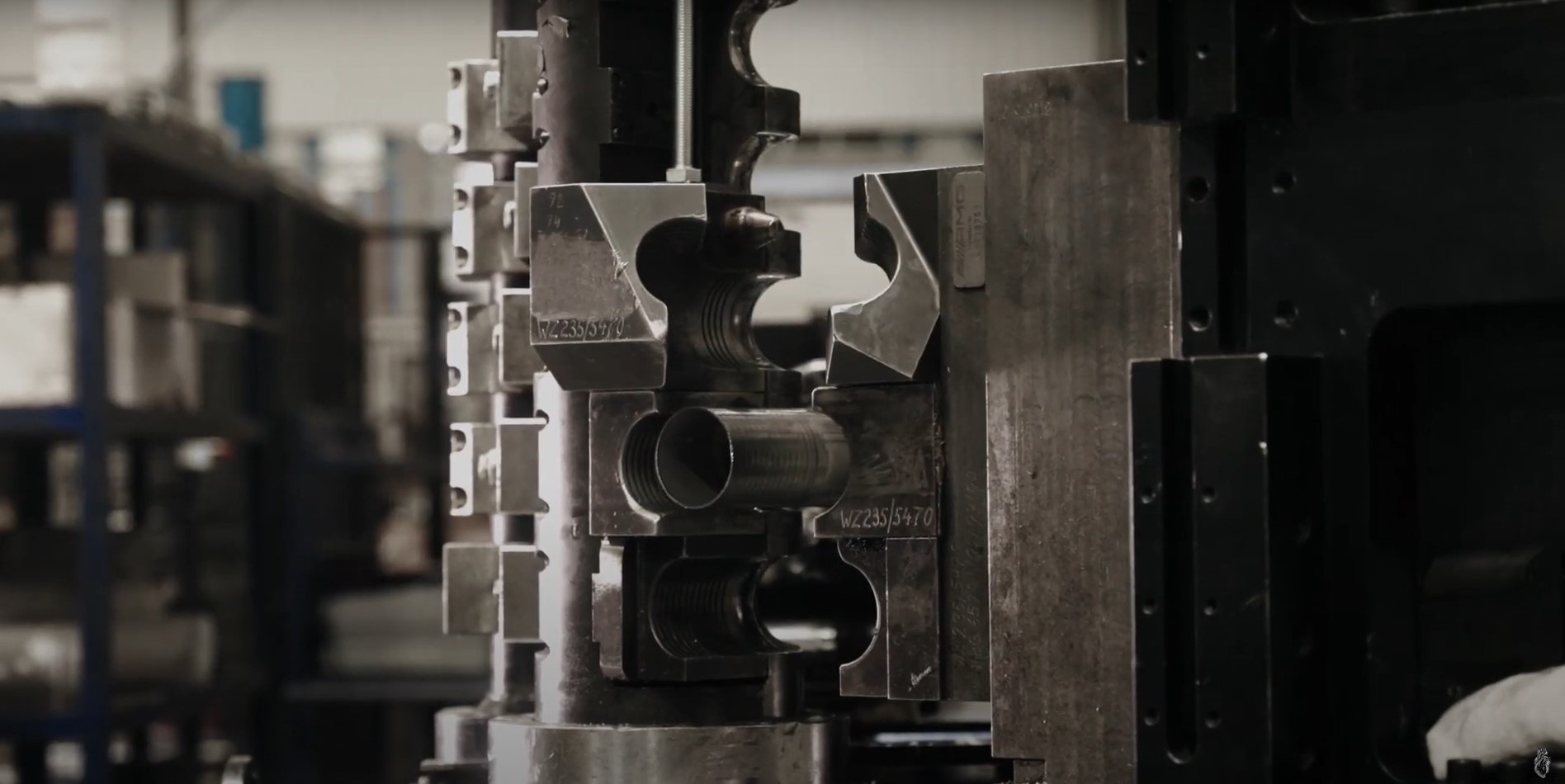
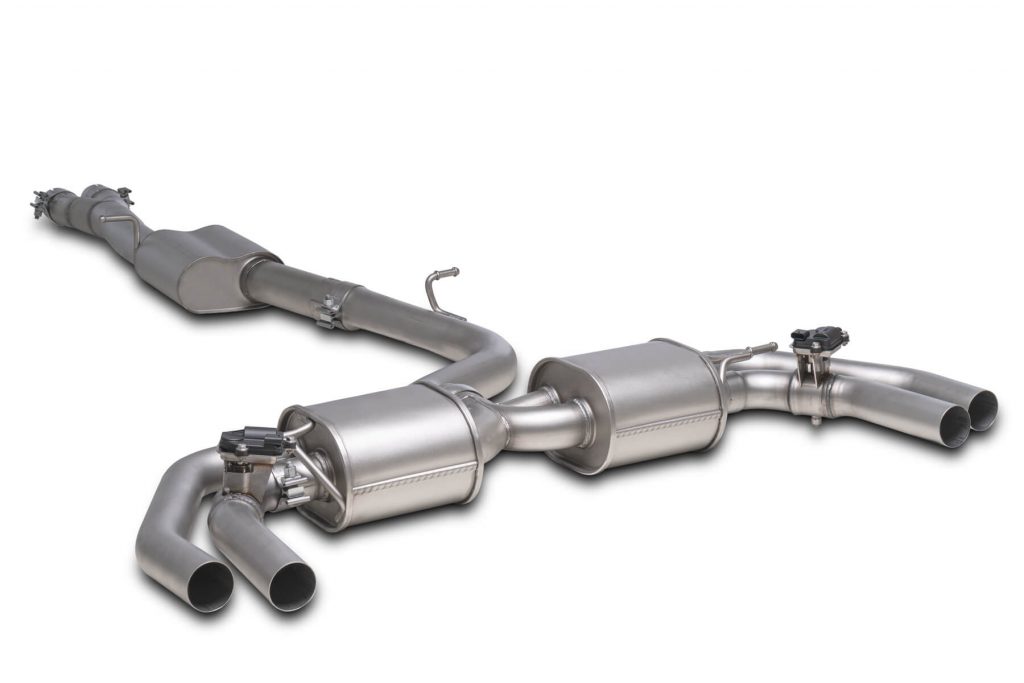
Automotive, Bicycle & Aerospace
Where we can help:
- Exhaust Systems: Bent tubes are used in exhaust pipes to bypass around vehicle components.
- Roll Cages: Tubes are bent to form the structural framework of roll cages for safety.
- Frame Construction: Tubing is bent to form frames for bicycles.
- Handlebars: Creating curved handlebars for bikes.
- Aircraft Frames: Tubing is bent to create frames and support structures in aircraft construction.
- Hydraulic Systems: Bending is utilized in creating tubing for hydraulic systems in aircraft.
Medical Equipment
- Support Structures: Tubes are to create support structures for medical equimpment
- Custom Components: Bending ist employed for manufacturing customized components in the medical field.
Quality Furniture
- Chair and Table Frames: Forming Frames for various types of furniture like tables, etc.
- Shelving Units: It helps to create custom shelving units with unique designs.
These applications demonstrate the broad range of uses for the tube bending industries where precision and customization are essential. Contact us today and schedule a first video-conference to learn more about our extensive competencies.
Our mission:
Optimized production
We optimize your processes. Costs are reduced. We are driven by quality and individuality.
Create value
Creating complex solutions for our customers is the most important thing for us – simply our core competence.
Tube bending FAQs
Optimizing tube bending for minimal defects involves understanding the interplay between material properties and desired bend geometry. Factors like material type, wall thickness, and diameter all influence bendability. Analyzing these alongside the desired bend radius and angle allows for adjustments like preheating the tube or using specific tooling. This careful approach minimizes defects like wrinkling or cracking, ensuring high-quality bends.
The most cost-effective tube bending method depends on your specific production run. High volume production with simple bends might favor automated CNC bending. For lower volume or complex bends, manual bending or specialized techniques like mandrel bending might be more economical. Considering setup time, machine costs, and potential for automation alongside material and complexity will help you find the sweet spot for your project.
Minimizing common bending errors like wrinkling and springback involves a two-pronged approach. First, we select the right tooling like wiper dies to prevent material bunching (wrinkling). Second, we optimize the bending process itself. This might involve adjusting the bend speed or using mandrels for tighter radii. Choosing the right material and potentially preheating it can also help reduce springback, the tendency of the tube to partially straighten after bending.
Selecting the best bending tool depends on the specific job and desired outcome. Dies are ideal for standard bends, while mandrels offer support for tighter radii and prevent collapsing. Wiper dies help control material flow and minimize wrinkling. After analyzing the bend geometry, material type, and required precision, we will guide you towards the most suitable tool for achieving proper part shape and quality.
When choosing a metal tube material for bending, we consider a balance between bendability and performance needs. Ductile materials like aluminum bend easily but might not offer the strength of steel. Conversely, high-strength steel might require more complex bending techniques. We analyze your application’s required strength, weight restrictions, and formability to select the best material for optimal bending and final product performance.