Metal Assembly & End of Line Testing
Component manufacturing and assembly in the metal forming industry involve the creation of precision parts through various shaping processes. Metal forming techniques such as stamping, forging, and extrusion are employed to mold raw materials into intricate components.
Precision is paramount, as these components often serve critical functions in diverse applications, from automotive to aerospace.
Assembly
In the manufacturing phase, raw metal materials undergo deformation processes, transforming them into specific shapes and sizes. This can include cutting, bending, or stretching to achieve the desired geometry. Precision machining may also be involved for intricate details.
Assembly is the subsequent stage, where these individual components are meticulously joined to construct the final product. Welding, fastening, or other joining methods are applied to ensure structural integrity and functionality. Rigorous quality control measures are implemented throughout, guaranteeing that each assembled component meets exact specifications.
The metal forming industry’s efficiency and success hinge on the seamless integration of manufacturing and assembly processes, ultimately delivering reliable and high-performance components for a multitude of industrial applications.
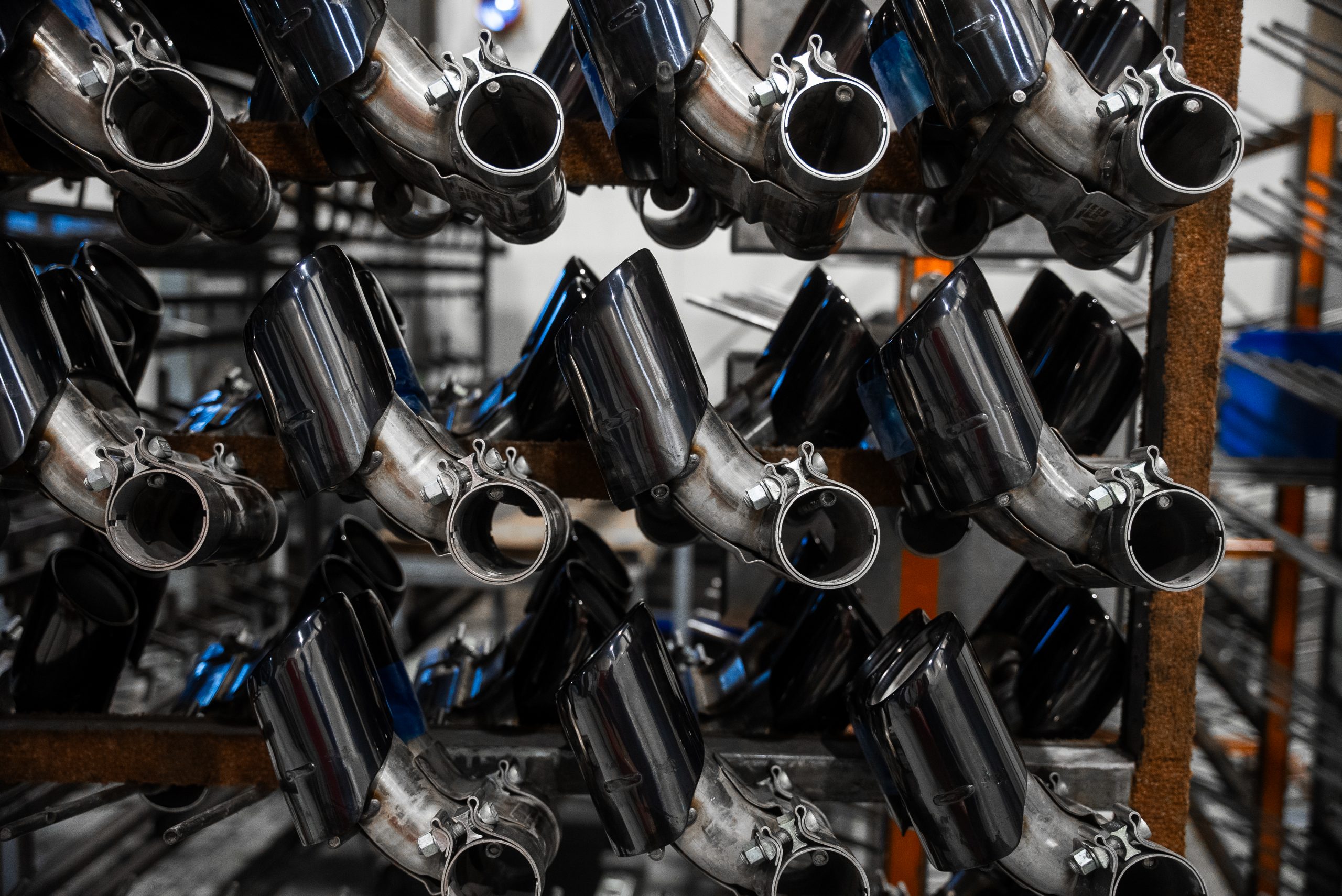
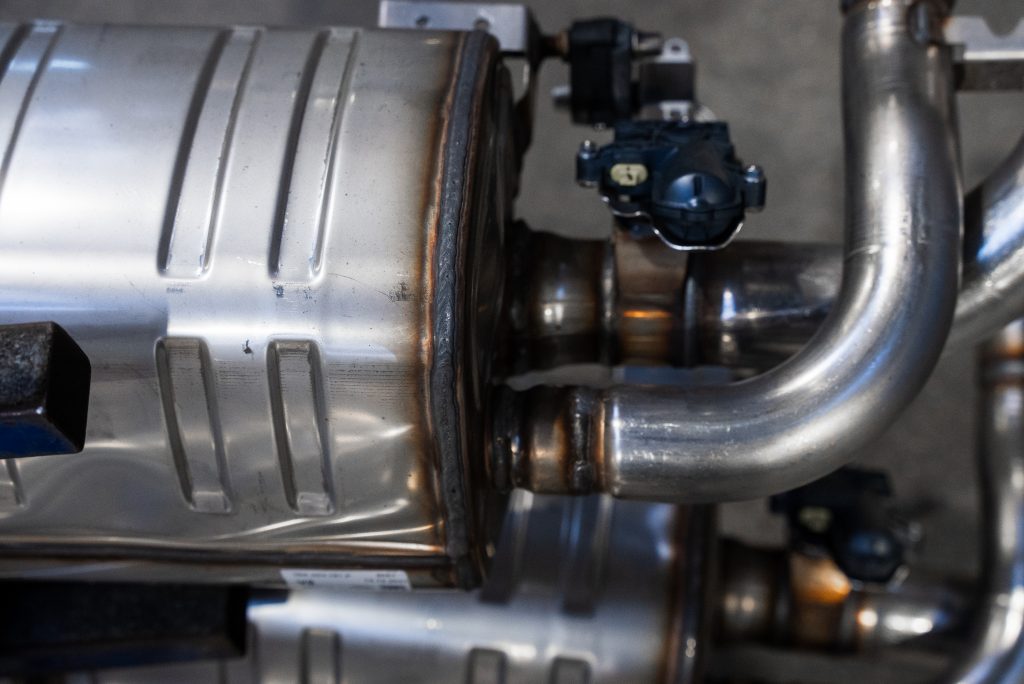
End of Line testing
End-of-line testing in metal forming component manufacturing and assembly serves as a crucial quality assurance step to ensure that the final products meet specified standards. This testing phase involves a comprehensive evaluation of the components to verify their integrity, functionality, and adherence to design specifications.
We especially focus on:
- Dimensional Accuracy: Precise measurements are taken to confirm that the components meet the specified dimensions. This ensures that the formed and assembled parts fit seamlessly into the larger structure or system.
- Material Integrity: End-of-line testing includes checks for material quality and structural integrity. This involves identifying any defects, such as cracks or imperfections, that could compromise the component’s durability and performance.
- Functionality Testing: Components are tested to verify that they perform their intended functions. This can involve simulations of real-world conditions to assess how the component behaves under stress, pressure, or other relevant factors.
- Surface Finish Inspection: The aesthetic and functional aspects of the components’ surface finish are examined. This is particularly important in industries where appearance matters, such as automotive or consumer electronics.
- Assembly Verification: If the components are part of a larger assembly, end-of-line testing includes checks to ensure proper alignment, fit, and interaction with other parts. This is essential for the seamless integration of components into the final product.
- Tolerance Checks: The components are tested against specified tolerances to guarantee that they can perform within acceptable limits. This involves assessing how variations in manufacturing processes may affect the final product.
- Performance under Stress: Components may undergo stress testing to assess their resilience and performance under extreme conditions. This is especially critical for components used in demanding environments, such as those in aerospace or industrial machinery.
- Quality Documentation: Comprehensive documentation of the testing results is essential for traceability and quality control purposes. This documentation provides a record of the testing process and the components’ compliance with standards.
End-of-line testing ensures that only components meeting stringent quality criteria move forward in the production process, minimizing the risk of defects and enhancing the overall reliability of the final products.
Our mission:
Optimized production
We optimize your processes. Costs are reduced. We are driven by quality and individuality.
Create value
Creating complex solutions for our customers is the most important thing for us – simply our core competence.
Assembly & Testing FAQs
Manual assembly: Here, the individual components are assembled by hand. This is the most commonly used method for the assembly of complex or sensitive products.
Semi-automated assembly: Some of the assembly tasks are automated using machines. This can increase the speed and efficiency of assembly.
Fully automated assembly: All assembly tasks are carried out using machines. This is the most efficient method for assembling products in high volumes.
Functional tests: This tests whether all functions of the product work properly.
Performance tests: This tests if the product fulfils the required performance characteristics.
Safety tests: They make sure the product fulfils the safety standards.
Visual inspection: This is where the product is checked for visible defects.
We frequently work with the automotive, aerospace and electronics industries. We also have expertise in the fields of mechanical engineering and medical technology.
Metal Competencies has many years of experience in the assembly and end-of-line testing of products in various industries. We have a certified quality management system and use state-of-the-art testing equipment to ensure the quality of our products.
Click on the link to the contact form above. Fill out the contact form on the website. A member of staff will get back to you as soon as possible.