Inert Gas Welding
Metal Inert Gas (MIG), Metal Active Gas (MAG), Tungsten Inert Gas (TIG or WIG), and Cold Metal Transfer (CMT) welding are widely utilized welding processes in automotive and related industries, each offering unique advantages.
From delicate jewelry to heavy pipelines, Inert Gas Welding offers unmatched control and quality. Dive in and discover its possibilities.
MIG & more
MIG welding employs a consumable wire electrode and a shielding gas, typically a mix of argon and carbon dioxide. It excels in high-speed applications and is commonly used for joining steel and aluminum components in automotive manufacturing. Its efficiency and versatility make it suitable for various thicknesses of materials.
Similar to MIG, MAG welding utilizes a shielding gas, but the gas composition can vary. It is particularly effective for welding materials like stainless steel and carbon steel. MAG welding is often preferred in situations where higher welding speeds are required, making it valuable in mass production settings within the automotive industry.
TIG or WIG welding relies on a non-consumable tungsten electrode and an inert shielding gas, typically argon. This process is known for its precision and ability to produce high-quality welds on thin materials. TIG welding is commonly used for intricate work in automotive applications, such as welding components with tight tolerances or welding aluminum parts in high-end vehicles.
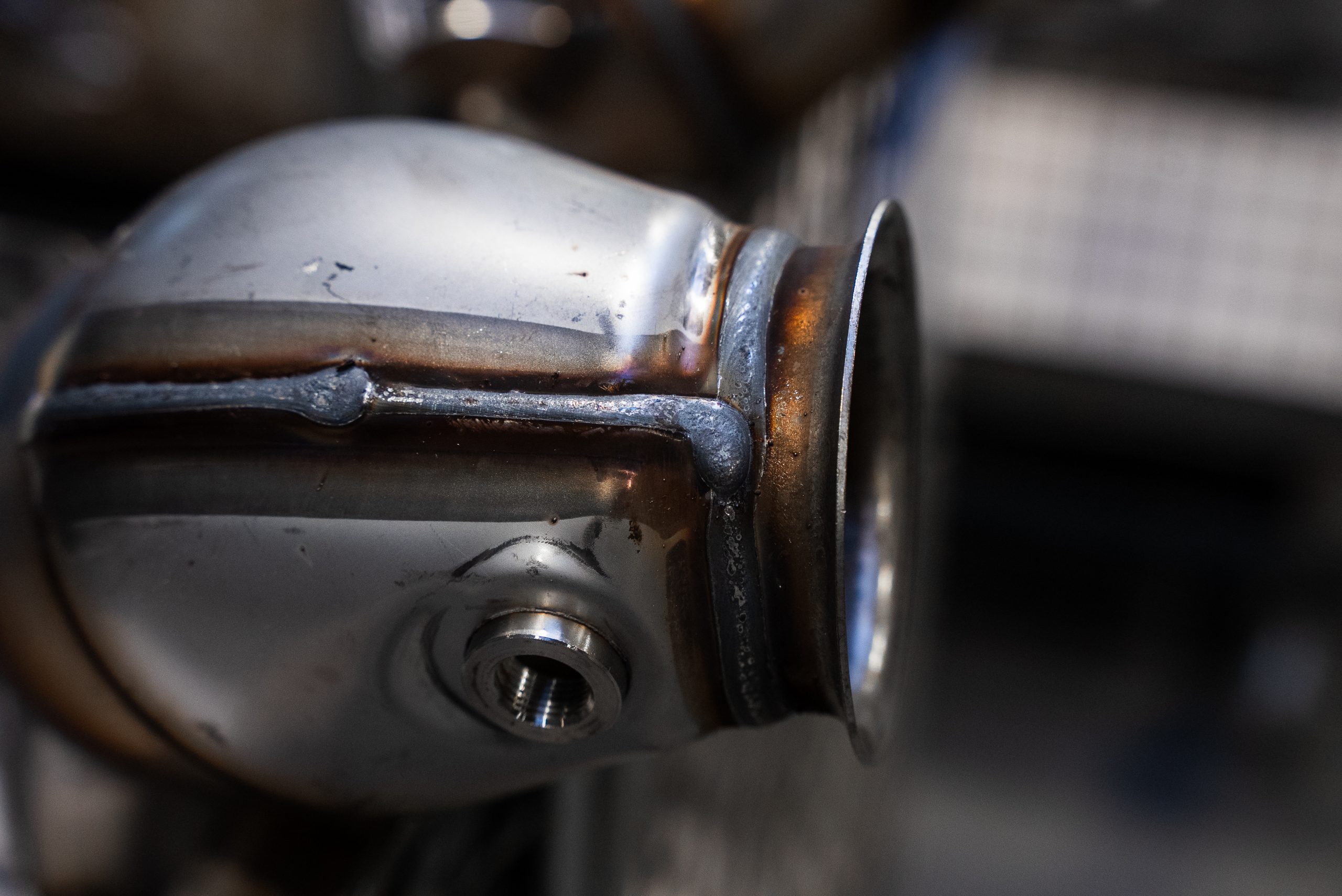
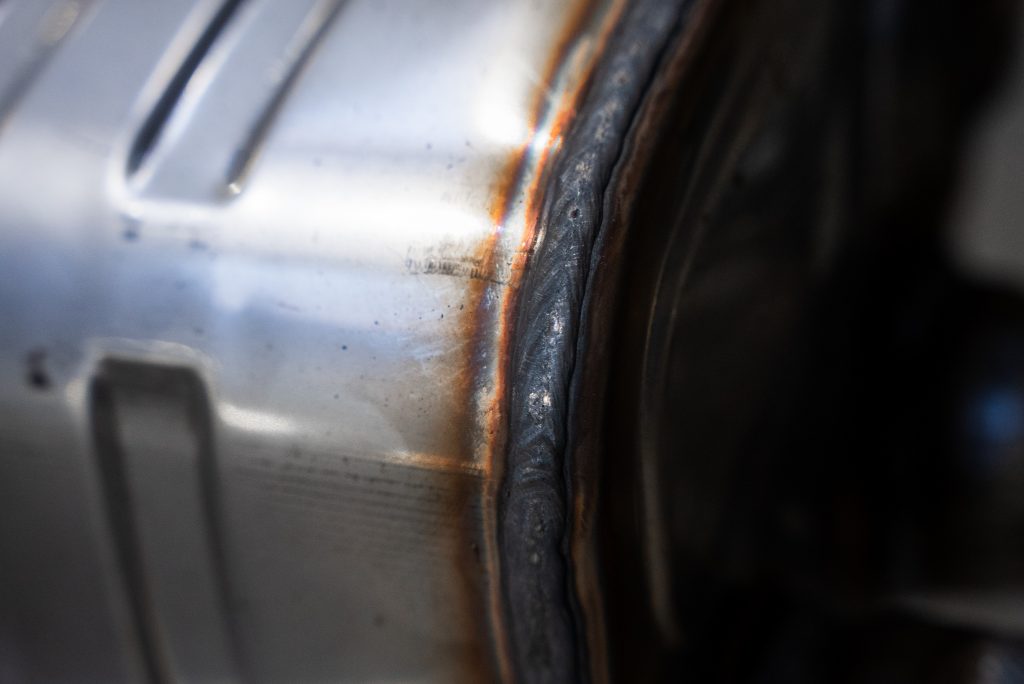
Cold Metal Transfer
Cold Metal Transfer (CMT) welding is a more recent innovation that utilizes a controlled short circuit to transfer droplets of molten metal. This process is particularly advantageous for welding lightweight materials, like aluminum, with minimal heat input. CMT welding is gaining popularity in the automotive industry for its ability to reduce distortion and produce high-quality welds on thin and heat-sensitive materials.
MIG and MAG welding are commonly employed for assembling vehicle frames and body components due to their speed and efficiency.
TIG/WIG welding is preferred for applications demanding high precision, such as welding exhaust systems and joining intricate components.
TIG/WIG and CMT welding find applications in welding aluminum components, which are prevalent in the automotive and aerospace industries.
MAG welding is favored in situations where high-volume production requires fast and consistent welding, contributing to the efficiency of assembly lines.
The choice of welding process in automotive and related industries depends on the specific requirements of the application, material, and desired welding characteristics, with each method offering distinct advantages in different scenarios.
Our mission:
Optimizing your production
We optimize your processes. Costs are reduced. We are driven by quality and individuality.
Adding value
Creating complex solutions for our customers is the most important thing for us – simply our core competence.
Inert Gas Welding FAQs
Gas-shielded welding, also known as MAG welding (Metal Active Gas) or MIG welding (Metal Inert Gas), is a welding process in which an electric arc is used to melt two workpieces while a shielding gas protects the welding area from oxidation. The shielding gas can either be an active gas such as carbon dioxide, which can alloy the weld seam, or an inert gas such as argon or helium, which protects the weld seam from contamination.
High quality weld seams: Gas-shielded welding can produce high quality weld seams with low porosity and cracking. Versatility: It can be used to weld a variety of metals, including steel, stainless steel, aluminium and copper. Ease of use: It is relatively easy to learn and use. Portability: Gas shielded arc welders are relatively small and portable, so they can be used for on-site applications.
Gas-shielded arc welding offers convincing advantages in three areas: Cost efficiency, quality and productivity. It scores with lower material losses, cleaner weld seams and lower energy requirements. The process is characterised by high seam quality, less deformation and versatility. Fast welding times, high deposition rates and simple operation increase productivity enormously. Gas-shielded welding therefore offers an attractive solution for various applications in different industries.
Gas-shielded welding is suitable for a wide range of materials, including steel, aluminium, copper, nickel alloys and more. Weldability, the availability of welding consumables and the experience of the welder play an essential role.
Pores, inclusions, cracks, overlaps and craters can occur during gas-shielded arc welding. They are caused by moisture in the gas, incorrect parameters, inadequate technology, unclean workpieces or unsuitable welding consumables. They can be avoided by using clean gas, correct parameters, clean workpieces, suitable filler materials and trained welders. Additional measures such as pre- and post-heating and non-destructive testing can further improve quality.